Custom Molded Products
In many applications, rotationally-molded products are more cost-effective than composites, metal, or other forms of thermoplastic processing. Other manufacturing methods may cost up to three times more than rotomolding!
What is Rotational Molding?
Rotational Molding is a high-temperature, low-pressure plastic-forming process that uses heat and biaxial rotation (angular rotation on two axes) to produce hollow, one-piece parts. The mold rotates at all times during the heating phase to maintain even thickness throughout the part, and during the cooling phase to prevent sagging or deformation.
Rotomolding is the cost-effective choice for manufacturing large, hollow parts such as oil tanks. The molds are significantly cheaper than the tooling required for alternate manufacturing procedures. Very little material is wasted during rotomolding, which makes the process both economical and environmentally-friendly. Since they require less tooling, molds may be built and put into production quickly, which makes rotational molding the preferred process for rush deliveries. This is especially true for complex parts.
Rotational molding: The mold rotates at all times during heating to maintain even thickness throughout the part, and during cooling to prevent sagging or deformation.
Advantages of rotomolded parts include:
- Design flexibility—Molded‑in threads or metal inserts may be added at little or no cost
- Lightweight—Parts may weigh up to 60% less than comparable metallic or composite parts
- Integrity—Consistent distribution of plastic compound within the mold provides uniform wall thicknesses, even when manufacturing complex geometry. Uniform wall thickness provides a smooth interior finish, an important factor in achieving superior fluid flow.
- Durability—Consistent wall thickness with strong outside corners is virtually stress-free. Large stretched sections are nonexistent, which enables the production of long, thin panels.
At Moeller, we have explored the capabilities—and nuance—of rotational molding for more than 30 years. As a result, we offer you unrivalled engineering and production capacity. And, while it’s easy to say that service is vitally important to us—just about everyone says that!—our recent ISO 9001:2008 certification verifies that customer satisfaction is Priority One at Moeller.
We have produced custom floor structural supports, consoles for smaller aluminum boats, speaker boxes, and many types of fluid containment. The photos below suggest the range of possible custom configurations.
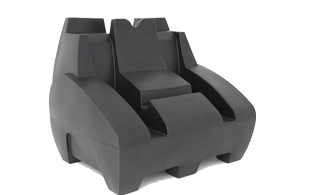
Hydro Hoist Boat Lift
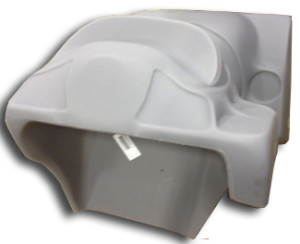
Console